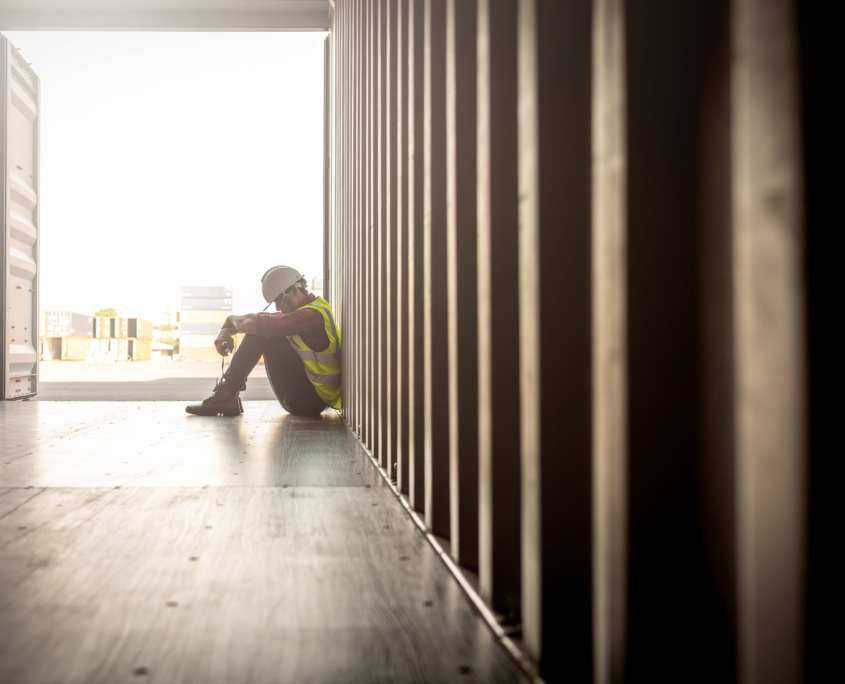
Stressed despair staff in logistic business sitting in container box at shipyard
Contents:
- Fatigue Across Industry
- Reducing Fatigue
- Determining Risk Exposure
- Determining Direct Accident Costs
- Adding it Up
- Implementing a Fatigue Risk Management Strategy
- Managing Fatigue Related Risks
As businesses seek to reduce expenses, a major source of savings can be easily overlooked. Without a risk management strategy, the costs associated with accidents and errors in the workplace can add up over time, significantly impacting the bottom line.
By anticipating and reducing risks, businesses can not only eliminate accidents that would threaten their operations, but they can also mitigate the impact of those accidents when they do occur. While every industry and organization will face unique risks, the human factor in business operations remains a constant.
In the same way that machines need regular maintenance to continue at peak capacity, a human workforce needs restful sleep to do their best work. However, fatigue from a lack of sleep contributes to more than just poor work. A worker experiencing fatigue in their workplace presents a risk to themselves and their colleagues.
In this article, we’ll be looking at some of the ways that fatigue contributes to risk in workplaces, and how the total costs of those risks add up. If you don’t already have a fatigue risk management strategy in place, by the time you finish reading you may be looking to implement one.
Fatigue Across Industry
Some organizations face risks from fatigue that are much more apparent than in other industries. Due to their shift-based work schedules, both transportation and heavy industry organizations are heavily impacted by fatigue, for example. For mature organizations, reviewing past accidents where fatigue was a contributing factor can easily put a direct dollar value on the costs associated with fatigue.
For organizations without historic data to draw from, or where physical accidents that halt production are less likely to occur, it can be more difficult to spot risks. Fatigue is complex, and the risks associated with impairment from fatigue are equally complex. With that said, due to the wide-ranging risks, any effective risk management strategy should include a fatigue risk management component.
Whether you’re seeking to reduce accidents with expensive heavy equipment or with data entry, mistakes in any capacity come with an associated cost. While costs vary across businesses and industry, the preventative measures to reduce risk are more easily assessed.
Reducing Fatigue
Because not all industry has the same level of easily accessed metrics, we’ll be taking a look at costs associated with fatigue in the transportation industry. Using the SAFTE™ Biomathematical Fatigue Model that also powers ReadiAnalytics™ by Fatigue Science, the US Department of Transportation found a direct correlation between SAFTE Alertness Score and accident propensity.
Not only were accidents were much likelier when a subject of the study had a lower SAFTE Score, indicating a high level of fatigue, but they were more costly as well. Accidents among fatigued subjects proved to be up to 5 times as costly as those from their better-rested colleagues.
Determining Risk Exposure
When an organization begin to look at fatigue risk exposure, there are many types of accidents and associated costs to consider. Some of the possible considerations include industry, type of accident, and whether you’re examining the direct or the indirect costs.
For a simplified example, we’ll be looking at the direct costs associated with lost-time incidents (LTIs) in the Oil & Gas industry. Our example begins with an Oil & Gas company with 5.34 total LTIs per 1,000 workers annually:
- If half of the LTIs in the company are fatigue-related, that’s 2.67 fatigue-related LTIs annually.
- Due to scheduling, in an industry-standard Oil & Gas company, about 16% of duty hours are fatigue-impaired.
- In a typical organization, 1,000 workers will work about 2,000,000 hours annually. Using our 16% industry-standard figure, that means about 316,000 fatigue-impaired hours are worked every year.
- Looking at the estimated LTIs in our example organization, this means that 2.67 LTIs will occur for every 316,000 fatigue-impaired hours that are worked.
Determining Direct Accident Costs
As noted earlier in the example of the transportation industry, fatigue-related incidents tend to be much more severe, and therefore much more costly than those not related to fatigue. As accident costs vary largely by industry, we’ll continue onward with the example of an Oil & Gas organization.
As we’re continuing to look at direct costs only, we can find that the average direct costs of an LTI begin at $200,000 USD. To determine how these costs related to fatigue-related risks, we’ll continue our example by looking at the difference in costs related to fatigue-related incidents compared to non-fatigue related incidents:
- Although there will be some differences by industry, we know that the US Department of Transportation found a 5x multiplier in costs for incidents that were fatigue-related. Using this as a starting point, we can begin with a conservative 3x multiplier for our example.
- Using our earlier 50% estimate of fatigue-related incidents compared to non-fatigue-related incidents, and adding in a 3x multiplier for costs, our total equation leads us to see that:
$200,000 [average LTI costs] x 50% [fatigue-related LTIs] x 3 [fatigue multiplier] = $300,000 in direct costs
- These $300,000 USD average direct costs for an incident would include things like workers’ compensation costs, medical costs, and equipment damage.
Adding it Up
Looking at our example Oil & Gas organization, using the total number of hours worked while fatigued and the costs of LTIs over that time, the calculated costs come out to $300,000 USD for 1,000 workers annually.
While the direct costs alone for the risk related to fatigue in a typical industry are already significant, the indirect costs are much higher. Industry studies have shown the direct costs to be up to five times higher. Indirect costs can include things like damage to buildings, worksites, retraining, legal fees, and more. For our example then, the indirect costs related to fatigue risk come to $1,500,000 USD.
Adding together the total indirect and the total direct costs brings the associated costs related to fatigue risk in our example organization to a whopping $1,800,000 USD.
Implementing a Fatigue Risk Management Strategy
By implementing a fatigue risk management strategy across an organization, it’s possible to not only keep workers safer on the job, but to see a positive return on investment. While many fatigue risk management solutions are able to help detect fatigue within a workforce, A truly effective risk management strategy requires being able to plan for and mitigate fatigue before it happens.
Fatigue Science’s ReadiAnalytics software is designed specifically for leadership within organizations to track fatigue patterns across their organization so that they can use that information to make better-informed decisions.
From our earlier example, we can see that by knowing how fatigue is impacting an organization, it’s possible to shift resources, training, and schedules to actually reduce the risk of accidents. In situations where it’s not possible to entirely eliminate fatigue due to scheduling, ReadiAnalytics also indicates the most optimal time for high-priority work to happen throughout a worker’s shift.
Managing Fatigue Related Risks
Risk management doesn’t mean entirely removing risks from a workplace. Instead, it means identifying and controlling the risks that are present. Using our Oil & Gas example, we’ve seen that fatigue can be incredibly costly to organizations. In order to manage the risk associated with fatigue, it’s necessary to put in place controls that mitigate the fatigue within the organization.
Mitigating fatigue begins with understanding and anticipating it. Not all workforces will face the same risks or find the same solutions, but they can all benefit by implementing an effective risk management strategy.